1. Preparation
① Start the air compressor, the powder coating manufacturer let it run dry for a few minutes, then drain the filter and the oil and water waste at the bottom of the air bag, close the drain valve, so that the air pressure is maintained at 0. 5-0. 6MPa.
②Connect the prepared oxygen to the oxygen connector at the bottom of the handle, tighten the air cap seat by hand, turn the valve stem handle to the fully closed position, and then open the oxygen cylinder valve (the oxygen pressure is adjusted to 0. 4-0.5MPa) , Turn the valve stem wrench to the fully open position, place your finger on the air inlet of the acetylene connector at the bottom of the handle, and test whether there is suction. If there is suction, it means that the spray gun system is normal. , It should be eliminated and re-commissioned. When it is normal, return the lever wrench to the fully closed position.
③Connect the air pipe and the acetylene pipe to the connecting pipes under the handle respectively, open the air valve on the filter and the acetylene cylinder gas valve, and adjust the acetylene pressure to 0.07-0.1MPa.
④Before ignition, turn the supporting screw wrench forward to separate a pair of wire feed rollers until a metal wire can pass, and then plug the required spray wire from the rear duct, pass through the nozzle, and extend in front of the air cap. Out of 6-8mm, reverse the support screw wrench to make a pair of wire feed rollers clamp the wire. The clamping force is adjusted by a spring shell on the left and right of the gear box. The more the spring shell is rotated inward, the greater the clamping force, and vice versa. The clamping force depends on the hardness of the sprayed wire. Generally, it is better to clamp until the wire can be fed smoothly and evenly.
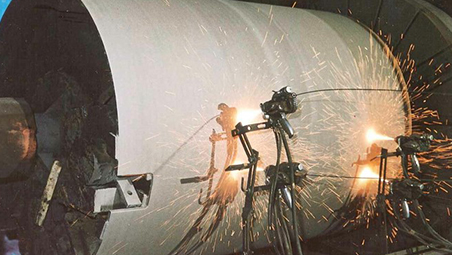
2. Ignition
① Rotate the valve stem handle 180° clockwise, and immediately turn the valve stem handle to 90° after the three-way gas is fully opened. At this time, a steel ball in the valve stem shell falls into the "v" groove of the valve stem (Neng Xin When you reach it or feel it with your hand), it is the ignition position. The flint gun or other safety fire is ignited in front of the spray gun. After ignition, slowly turn the handle of the valve stem to 180. That is, in the fully open position, molten metal sparks appear in front of the spray gun.
② Adjust the intensity of sparks. In order to achieve the ideal coating and excellent spraying efficiency and make full use of the gas heat energy, it is necessary to adjust the wire feeding speed and gas flow rate. If the acetylene gauge pressure of the powder coating manufacturer is stable at about 0.8 MPa and the air pressure is not less than 0.5 MPa, there is generally no need to adjust it, just adjust the oxygen pressure and wire feeding speed. Take spray steel as an example: when the steel wire is normally melted, its melting end should be level with the air cap outlet plane. If the melting end exceeds the air cap, the wire feeding speed is too high, or the wire feeding speed is too slow in the air cap. It should be adjusted to the normal wire feeding speed by the speed control dial. At this time, if the fire bouquet is not dense or the sparks are scattered, the oxygen pressure regulator should be adjusted to achieve a dense and dense fire bouquet. But when spraying zinc or aluminum wire, the melting point can extend out of the air cap. The length depends on the thickness of the coating particles.
3. The operating parameters have the same operating parameters for any spraying method. Except for plasma spray welding, although the operating parameters are not very strict, they must be controlled within a certain range, otherwise the coating quality and deposition efficiency will be affected.
① Spraying distance. Spraying distance refers to the linear distance from the nozzle end to the surface of the substrate. The spraying distance is the distance that the sprayed particles fly. During the stroke, its speed and temperature will change. The speed of the particle first accelerates and then decelerates. The temperature of the particles decreases as the distance increases. Therefore, when the spraying distance is too large, the temperature and kinetic energy of the particles hitting the surface of the substrate are not enough to produce sufficient deformation, reduce the bonding strength of the coating, and cause more particles to rebound and lose, which reduces the deposition efficiency. Affected by the surrounding atmosphere in many places, oxidation tends to be serious, resulting in an increase in coating oxide slag. If the spraying distance is too small, the particles stay in the heat source for too short time to be sufficiently heated or accelerated, which also affects the quality of the coating, and the surface of the substrate will overheat due to the high temperature area of the heat source. Therefore, the spraying distance should be controlled within a certain range according to the specific conditions of the spraying heat source, spraying materials, etc., generally 100-180mm.
② Spray angle. The spray angle refers to the angle between the spray jet axis and the tangent to the substrate surface. Controlling the spray angle is required by the directionality of the spraying process. The spraying angle cannot be less than 45°, generally 60°-90°.
③ The moving speed of the spray gun and the workpiece. The moving speed of the spray gun refers to the speed at which the spray gun moves along the surface of the substrate during the spraying process. Through the relative movement of the spray gun and the workpiece, the coating is deposited on the surface of the substrate.
When the spraying rate and deposition efficiency are determined, the relative moving speed of the spray gun and the workpiece determines the thickness of the coating in the past spraying. In order to obtain a uniform coating structure, the thickness should be controlled within a certain range, depending on the spraying method and spraying materials. The thickness of each pass of flame spraying is 0.1-0.15mm, and the thickness of each pass of plasma spraying is generally less than 0.05mm. According to the requirements of each spraying thickness, select the correct relative movement speed of the spray gun and the workpiece, generally 7-18m/min. Special attention should be paid not to cause local overheating of the substrate surface due to the slow movement of the spray gun. In order to obtain a thick coating, multiple sprays should be carried out.
For spraying cylindrical workpieces, it involves the rotation speed of the workpiece and the lateral movement speed of the spray gun. The rotation speed of the workpiece makes the linear speed of the workpiece surface meet the requirements of the relative moving speed of the spray gun and the workpiece. The lateral movement speed of the spray gun should take into account the thickness of the overlap of the coating under a certain pitch, so that the thickness of the coating on the cylindrical surface is uniform.
This article is reproduced from the Internet, if there is any infringement, please contact the website staff to delete it!